Compression applications are the most common use for volute springs, which are comprised of flat metal strips that are wound together to form helical spirals. The type of material, the diameter, the stroke, the intended application, and the type of end attachment are all important specifications. Volute springs are typically put to use in applications that call for a compression spring to have a particularly long fatigue life or a particularly high level of spring force repeatability. They are available in a range of sizes to accommodate the different materials, applications, and required levels of force. While others have two ends, single-ended volute springs are the most common type. The compression spring that can be found in the spring manufacturer is an example of an application of the volute spring that is very easy to recognize.
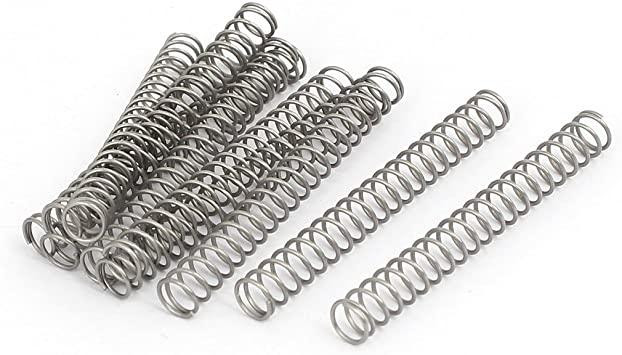
Garter springs are spring coils whose ends are joined to form circular springs. Garter springs are used to provide a radial force in components that may contain a variable load. Garter springs are formed by joining the ends of two separate spring coils. Garter springs are put to use in hydraulic, pneumatic, and radial shaft seals, where they provide a slight inward force on the sealing lips. Another common application for garter springs is in clothing.
When compressed or displaced, flat springs produce a repeatable counterforce that can be used for positioning or contacting purposes. Flat springs can be made from strips or bars of metal, or assemblies of such materials, and are formed to produce this effect. Among the most important specifications are the application that will be used, the type of flat spring, and the type of spring ends. Flat springs are most commonly put to use in applications that call for the application of a repeatable counterforce to control motion or load by means of making contact and exerting force. They can be purchased in a wide range of sizes, types, and materials, in addition to a number of different mounting types and shapes. Examples of flat springs that are easy to spot include the contacts on flat batteries, the leaf springs in vehicles, and the counterbalances in sliding screen windows.
Gas springs are mechanical devices that produce a force bias on a piston or rod by utilizing the pressure from a pre-charge of nitrogen or other inert gases. Gas springs consist of a cylinder and a rod, and they are powered by nitrogen or other inert gases. The application that it is designed for, the stroke, the compressed length, the extended length, the force, and the features are all important specifications. The majority of applications for gas springs can be found in the automotive sector, specifically in the process of elevating and/or lowering hoods and hatches. They come in a wide range of sizes, and the length of their stroke can be customized to meet the demands of a particular load and application. In addition to these applications, the material can also be used to adjust the seat height of office chairs.
Air springs are devices of the bellow or bladder type that are pressurized with air and come in a variety of shapes and sizes. They are utilized for the purposes of actuation, shock absorption, and vibration isolation. The intended application, type, style, physical dimensions, mounting type, and features are all important aspects to consider when determining the product’s specifications. The majority of applications for air springs are found in machines, such as vehicle suspensions for the purpose of shock absorption and machine mounts for the purpose of vibration isolation. They come in a wide variety of shapes and sizes, and the selection process is determined by the load requirements and the application. Additional applications include hoisting, compressing, tilting, and so on. Vibration isolation can be achieved with air springs, which are also referred to as air cushions.
The term “spring assembly” refers to the process by which springs are assembled into various components for use in various applications. Protective coil springs are the name given to springs that are used to protect hydraulic lines. Die springs are common places to find hydraulic springs because of their use of a specialized hydraulic fluid in applications with very short strokes. The mattresses on a bed are held up by the box springs.
Because compression springs have self-limiting properties, they are preferred over extension springs for use in applications that are particularly demanding. On the other hand, an extension spring can be easily overloaded to the point where it breaks, while a compression spring cannot be stretched beyond its breaking point. However, extension springs are suitable for use in a wide variety of circumstances because their range of travel is constrained by the installation itself. Take, for example, the numerous extension springs that are utilized in the operation of an automotive drum brake, an absolutely essential application.
In addition to the conventional straight coil, compression springs can be manufactured in a variety of other shapes, such as conical, barrel, and hourglass forms, which are utilized in specific applications. Even though they are typically made from round wire, compression springs can also be made from square or rectangular wires if necessary. Other than round coils, they can also be manufactured in shapes like rectangles and other irregular shapes. In addition to the standard form of the spring supplier, extension springs can also be formed into a variety of other forms.
The ends of compression springs and extension springs are essential components that must be taken into consideration. Seats frequently make use of coil springs, and grinding the ends of the springs flat enables them to fit completely within a seat. This is especially true of springs designed for heavy-duty applications, such as those found in the valve trains of engines. In comparison to the spring helixes, compression springs designed for applications requiring less force are typically constructed with a single extra loop at each end. This design allows the spring to lie flat. There is a wide selection of hooks and loops that can be attached to the ends of extension springs. These hooks and loops can be used to secure the springs to posts, holes, and other similar surfaces. In many cases, the spring will break at the hook rather than the coil if it is overloaded.
Music wire is just one example of the wide variety of spring steel alloys that can be used in the construction of coil springs. Some materials have favorable characteristics in terms of their resistance to relaxation, electrical conductivity, and corrosion. After being formed, coil springs are typically subjected to a stress-relieving process in order to remove any residual stresses that may have been introduced during the manufacturing process. Please refer to the related guide that we have written on the various types of spring materials for a more in-depth discussion on the various materials that are used in the production of springs.